Features of DPI' grinding
DPI can handle grinding as part of its integrated production.
Grinding is a technology in which a grindstone is rotated and applied to the product to scrape the surface and make it into a standard shape. We can also process various materials, shapes, and sizes. Because we cut little by little, we have high dimensional accuracy and are able to process high-hardness materials that are difficult to cut. This technology is especially applied to parts that require precision, such as compressor-related parts.
We have barrel polishing and surface grinding equipment. Depending on the characteristics and specifications of the product, we smoothen surfaces that have been hardened by heat treatment, or apply compressive residual stress created by applying a polishing stone to the surface of a product to increase its strength.
Barrel polishing
Rotating barrel
When the tumbler containing the product, polishing stone, grinding chemicals, and water is rotated, the product rubs against the polishing stone and is polished. We often use this technique to round the edges of the inner and outer diameters of ring-shaped products. We have a 500 L machine and can polish 300 products with an outside diameter of 120 mm at a time. We can also handle products that are large in size and in large quantities.
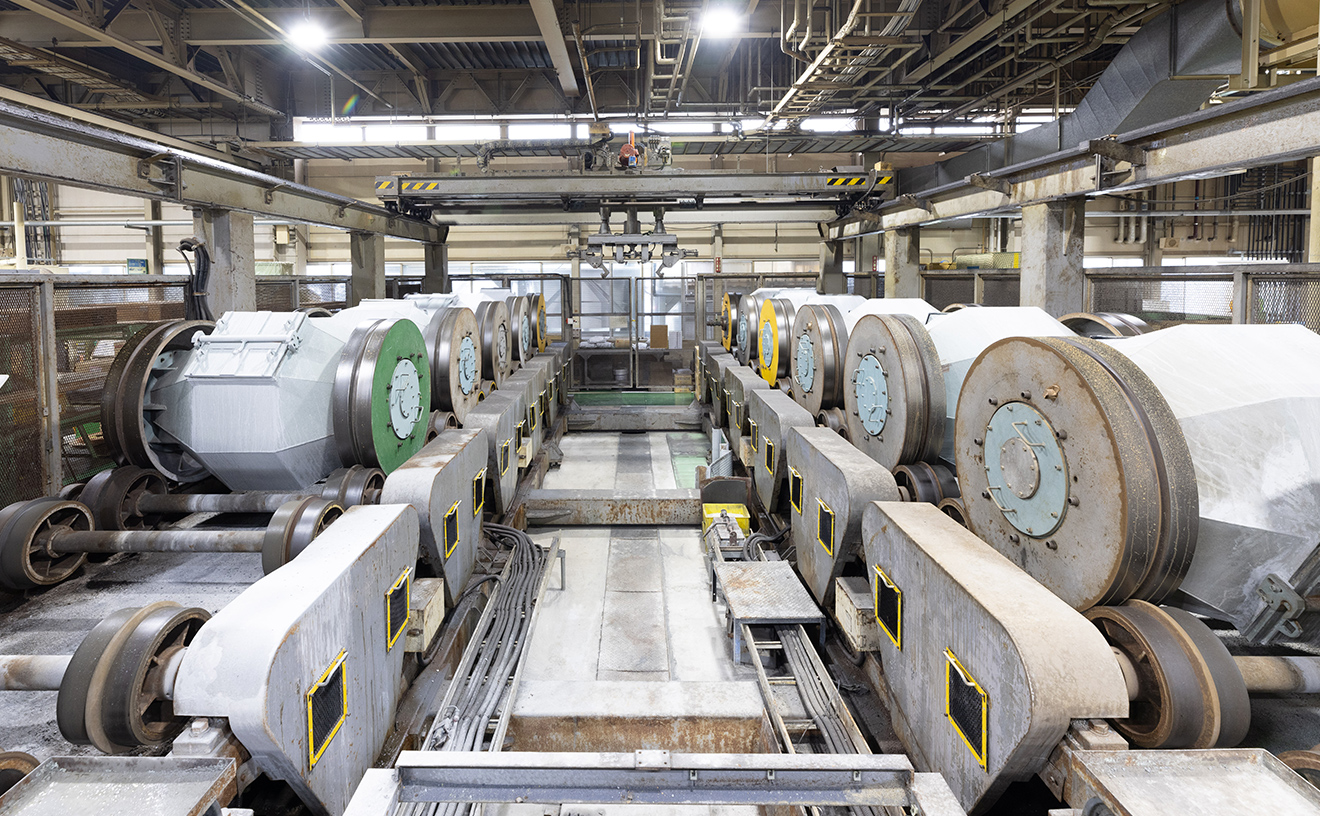
Centrifugal barrel
We use a combination of revolution and autorotation to rotate four barrel tanks at high speed, applying high pressure generated by centrifugal force to the products and polishing stones in the tank for polishing. Since it can be done in a short time, we use it for deburring and surface finishing of relatively small products.
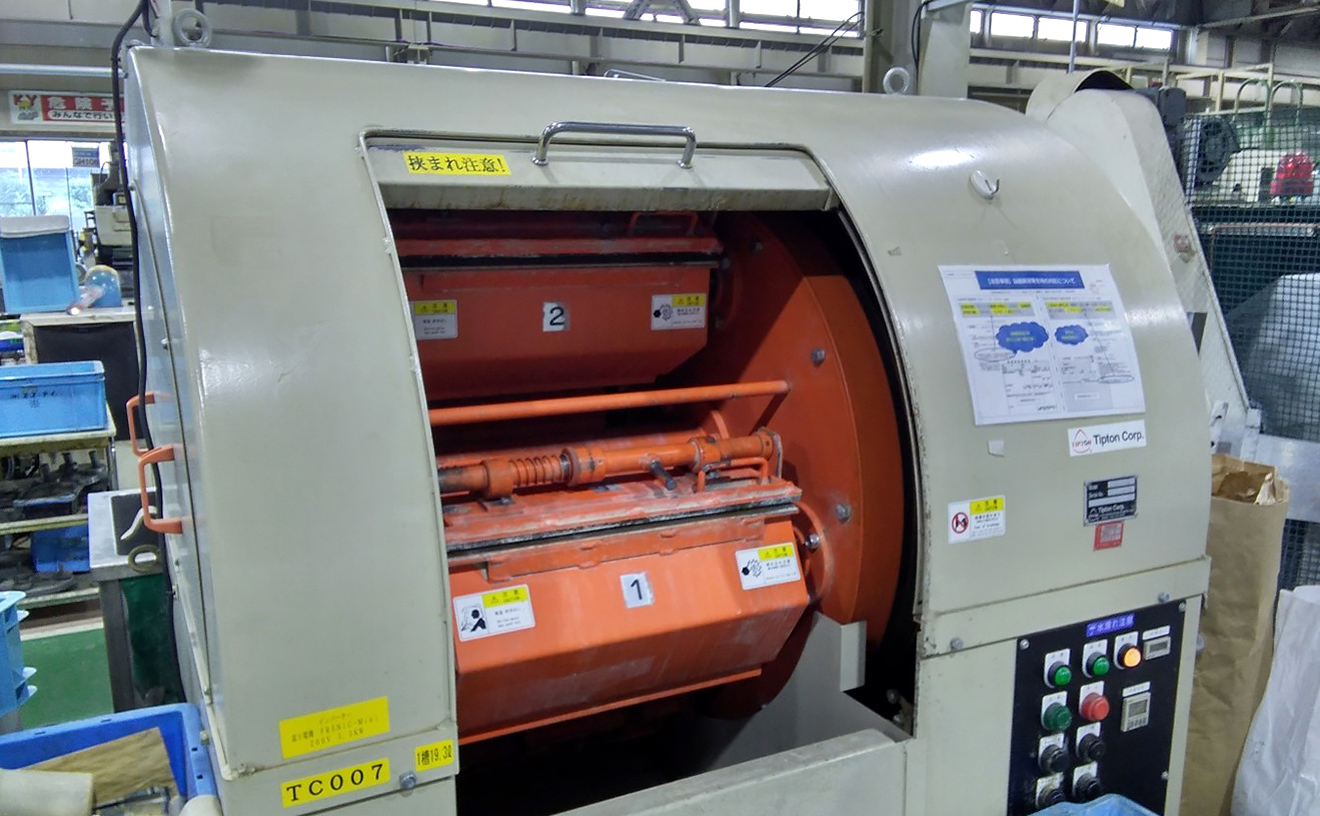
Vibratory barrel
It is a method of polishing products by creating a fluidized bed in a barrel tank through fine vibrations. Although it can be used for round chamfering and corner deburring, we mainly use it for finishing because the polishing condition can be visually checked.
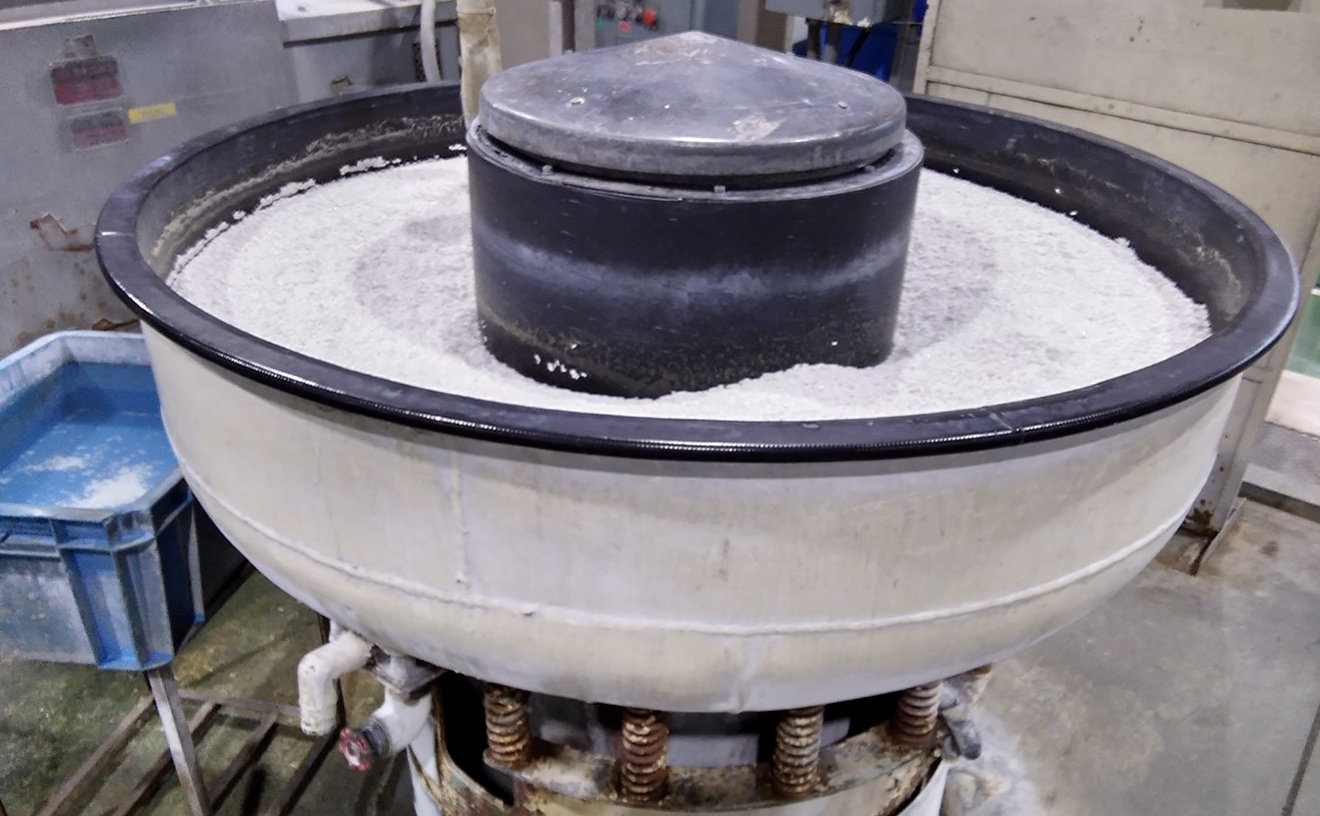
Roll flow
It is equipment that automatically polishes the product by placing it in a bucket and setting the rotation speed. We use it for round chamfering and deburring ring-shaped products.
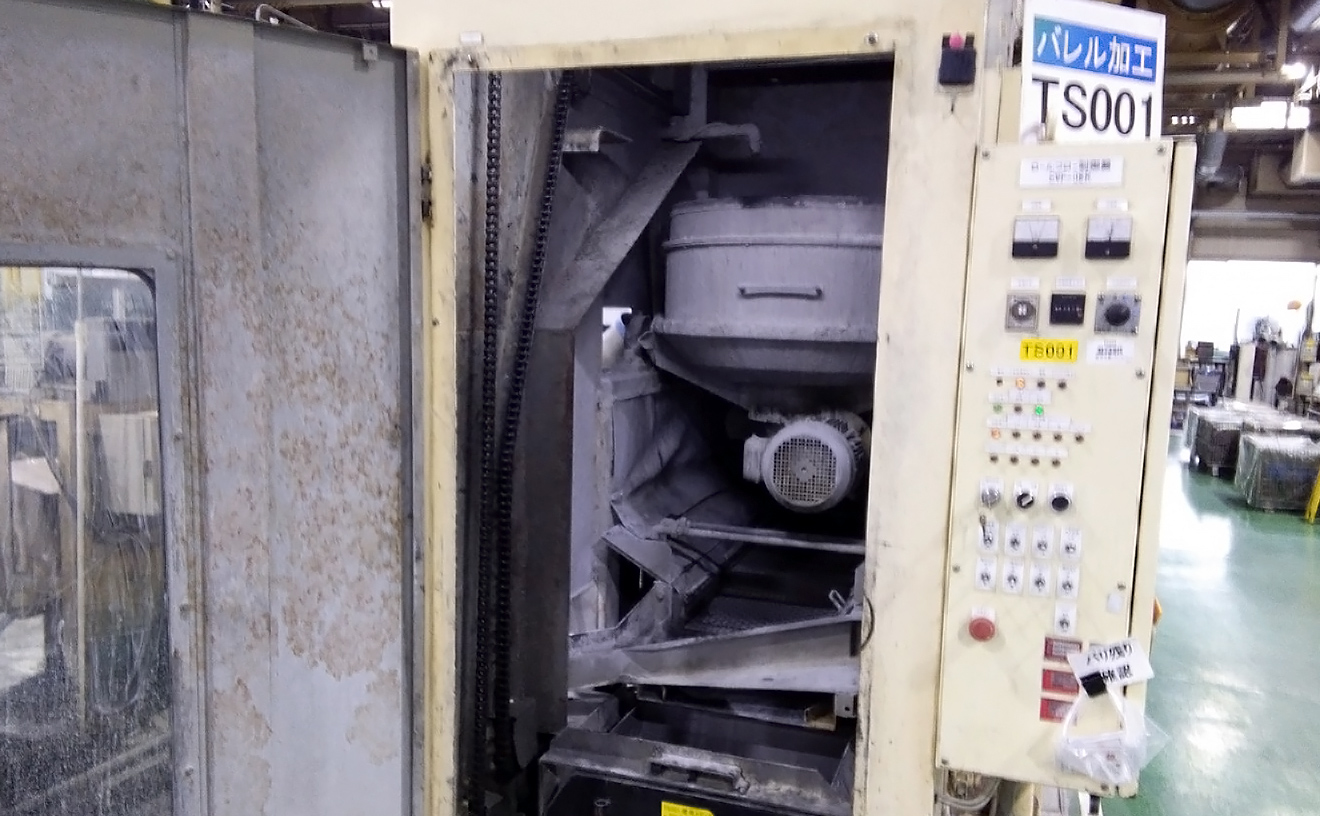
Surface grinding
Vertical grinding machine
The product is fixed on a magnetic table, and the grindstone installed at the top and the table at the bottom rotate in parallel to polish the product one side at a time. A relatively large amount of product can be polished. You can also control the cutting method by changing the material of the grindstone.
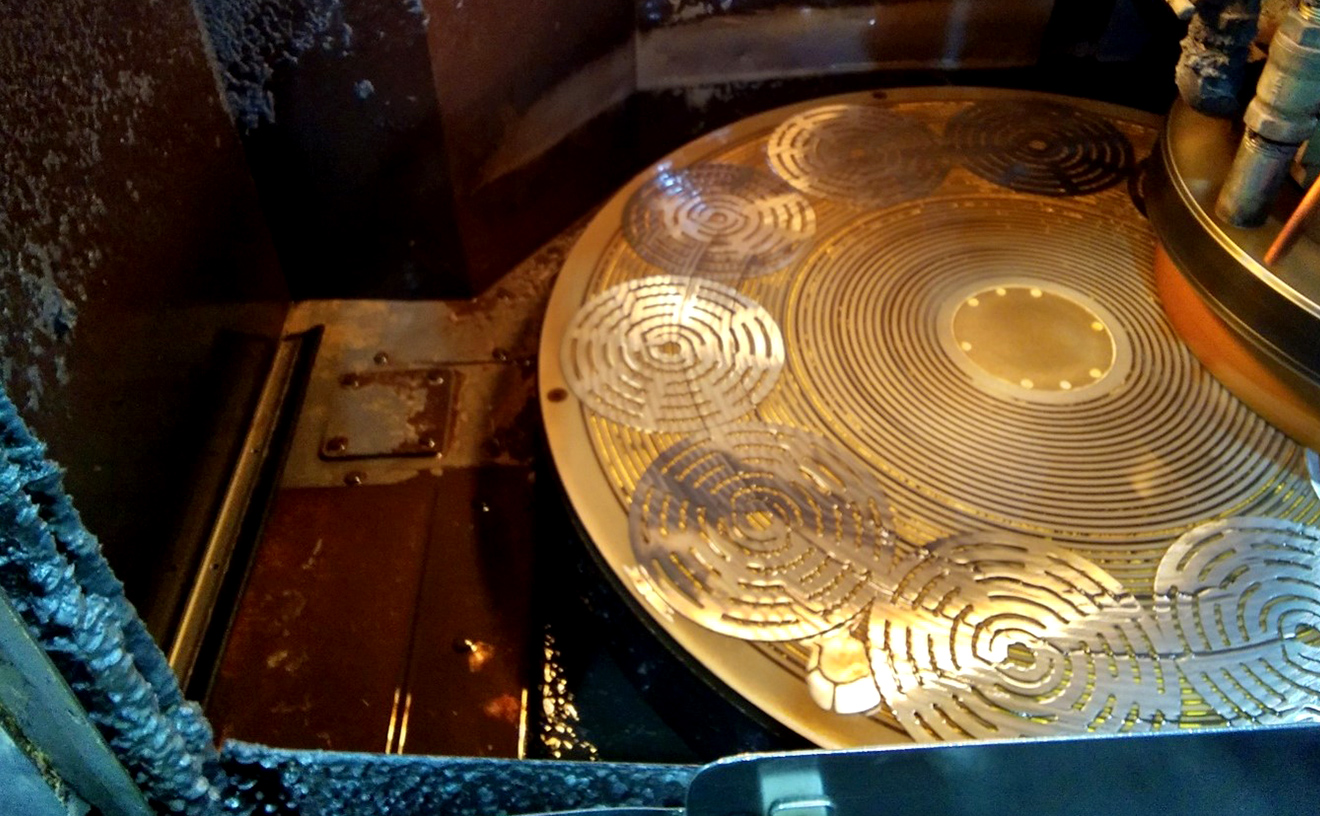
Rotary grinding machine
This is a small version of a vertical grinding machine that is suitable for finishing surfaces neatly.
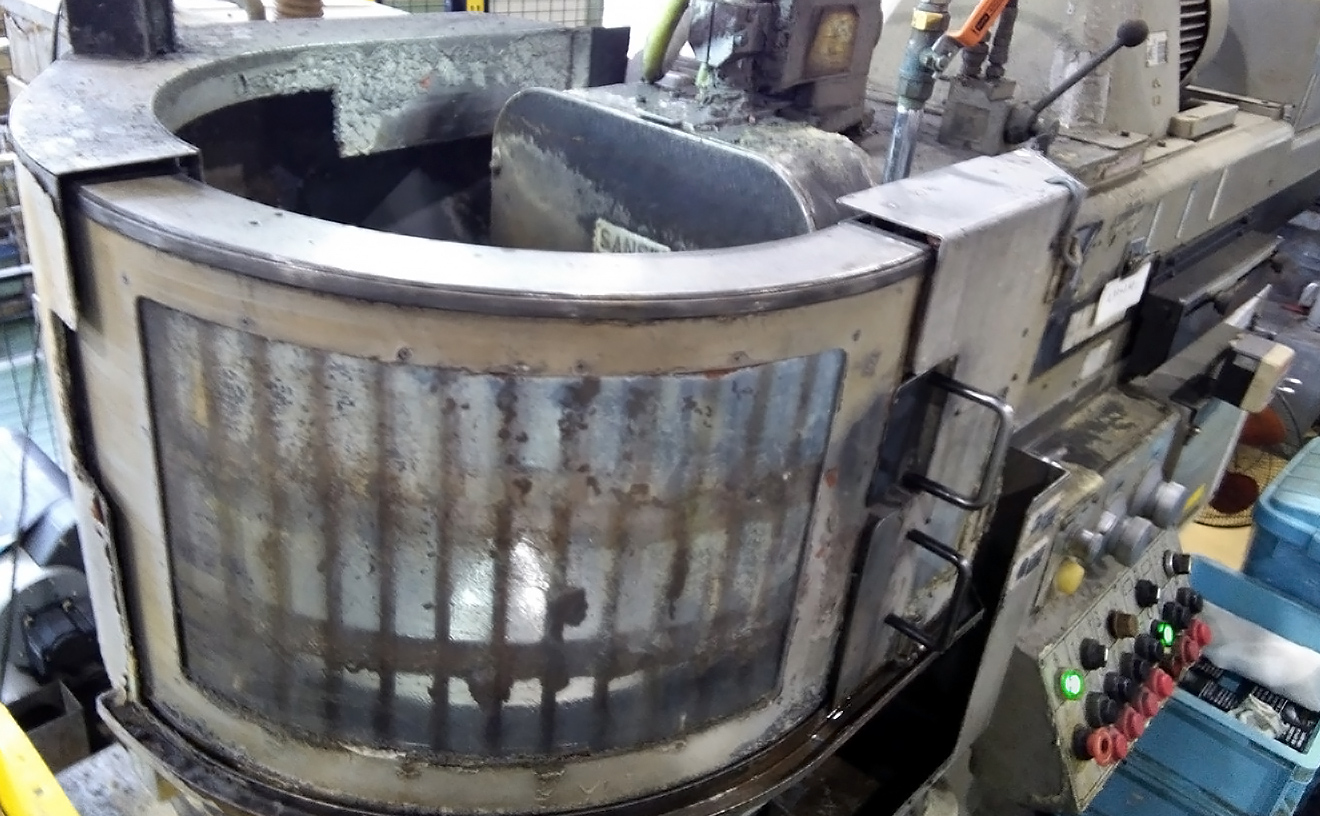
Double head grinding machine
It installs grindstones at the top and bottom, and can grind both sides of the product at the same time. Suitable for processing products that require both sides to be polished in the same way.
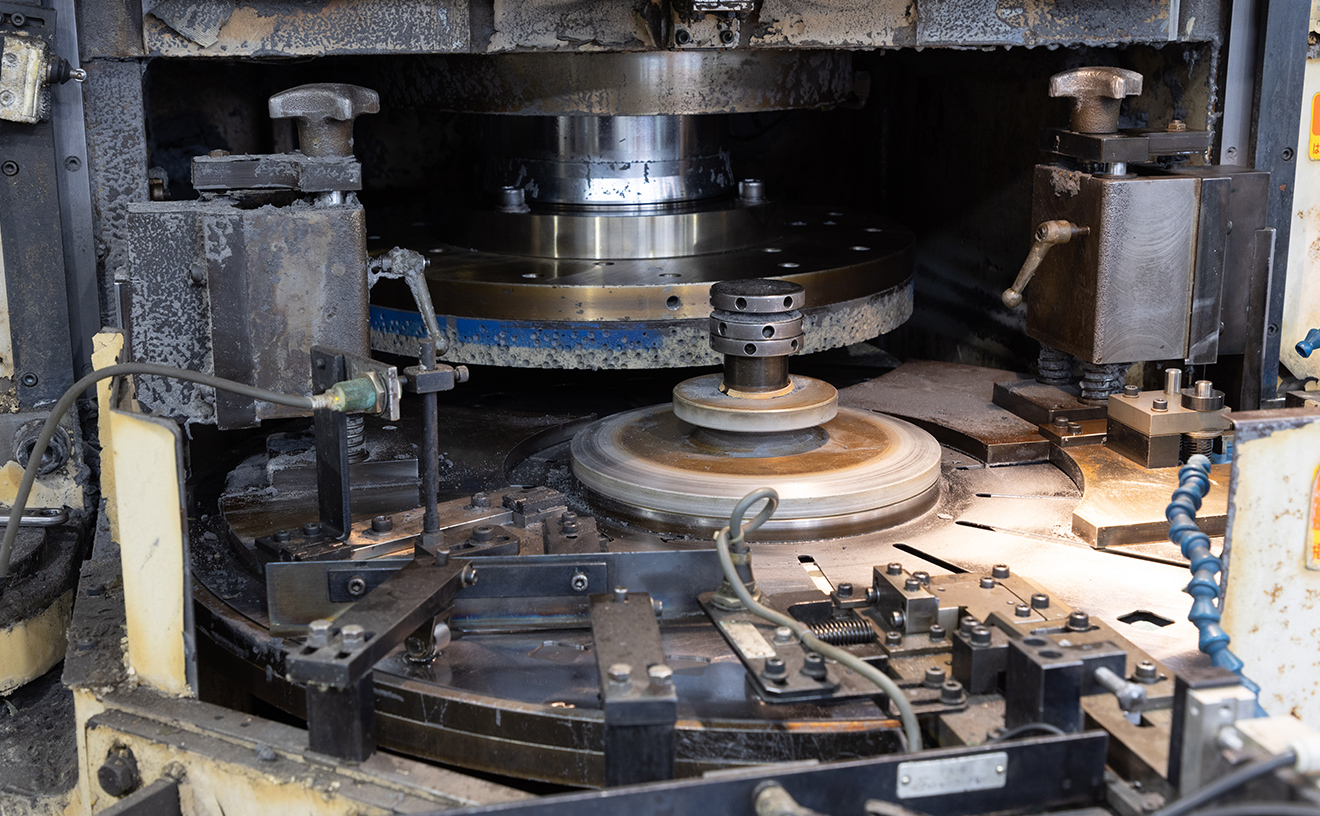
High pro lapping machine
It installs grindstones at the top and bottom to polish the product. Since the product is polished semi-automatically without using magnetism, it is also possible to handle materials that are not magnetic. In recent years, it has been used for grinding stainless steel (SUS type) materials.
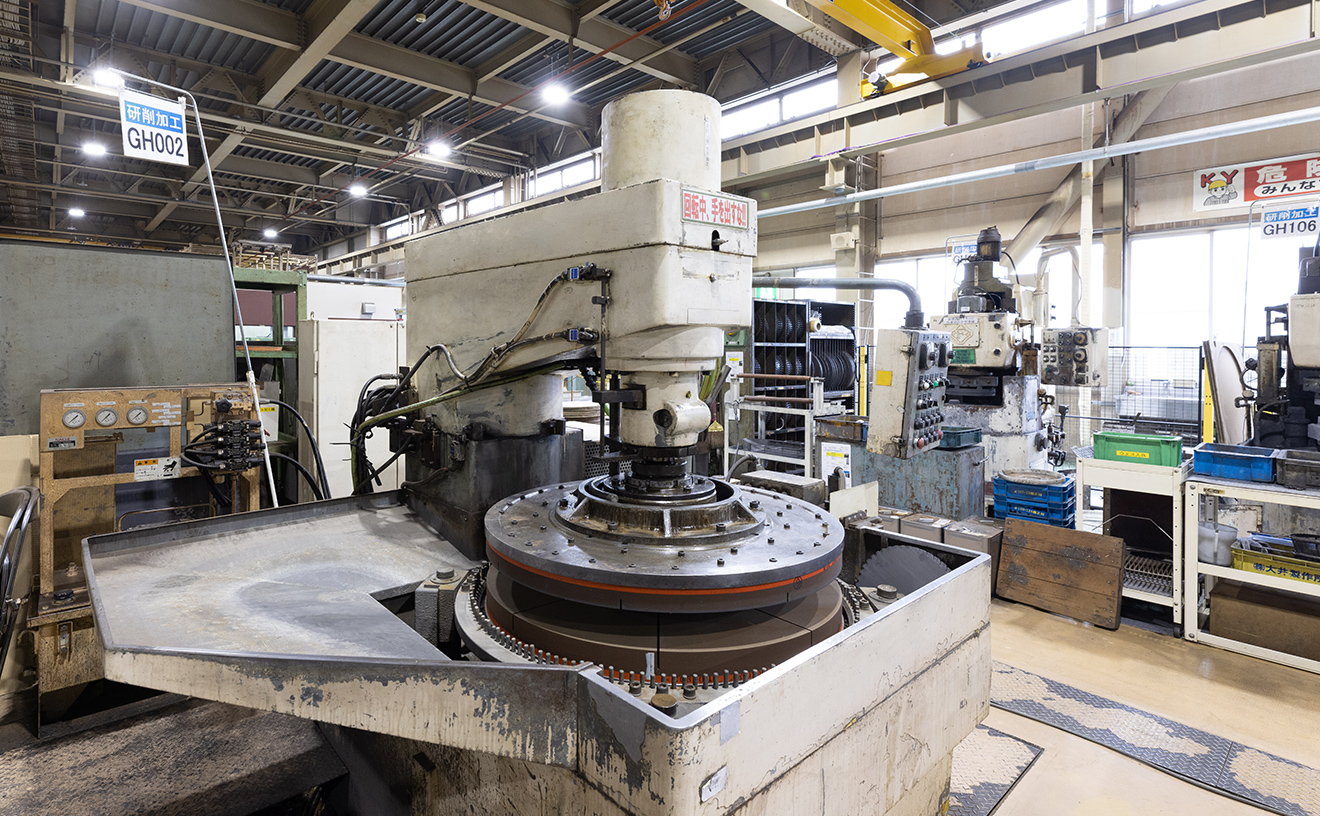
Others
Lapping
Place the product on a surface plate, add abrasive grains, and grind while rotating the entire machine.
It is often used for the final finishing of compressor parts.
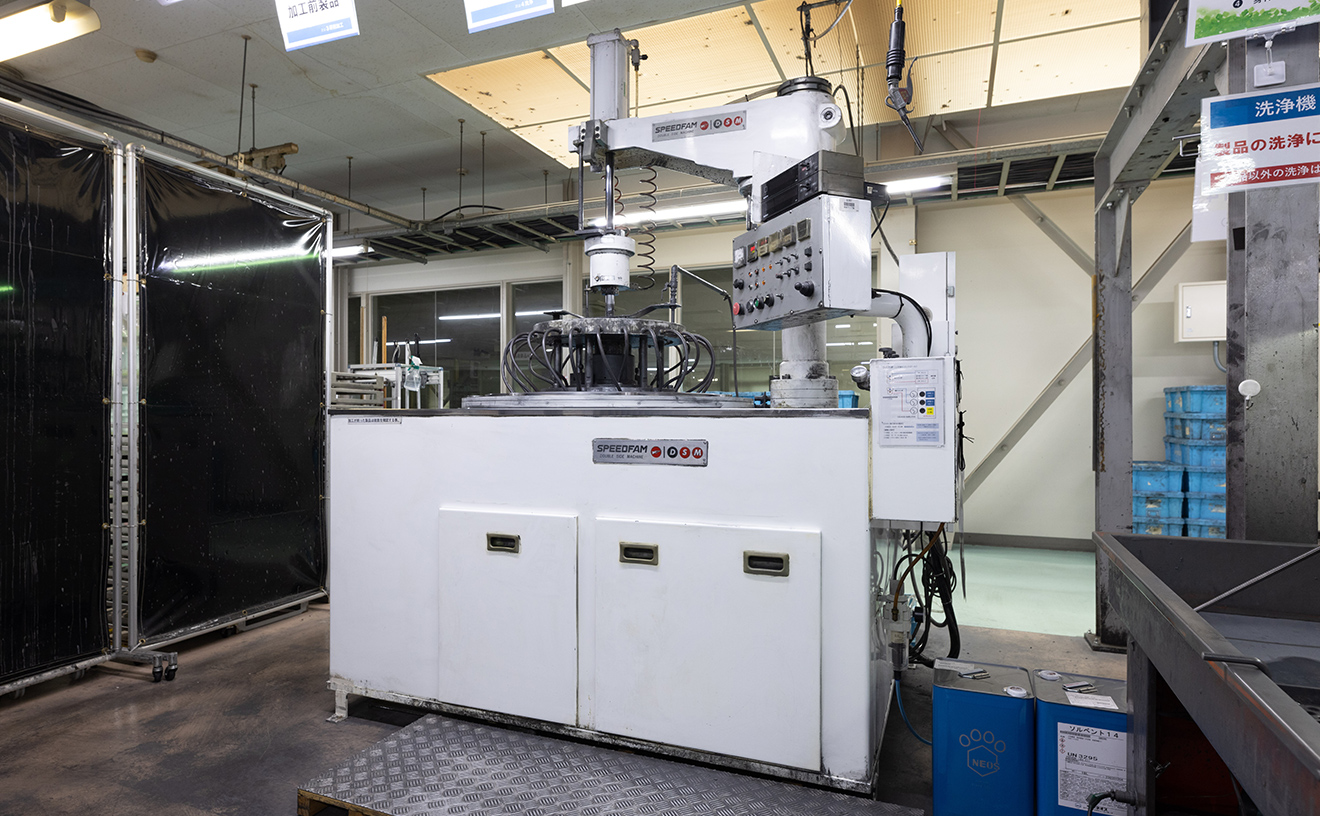